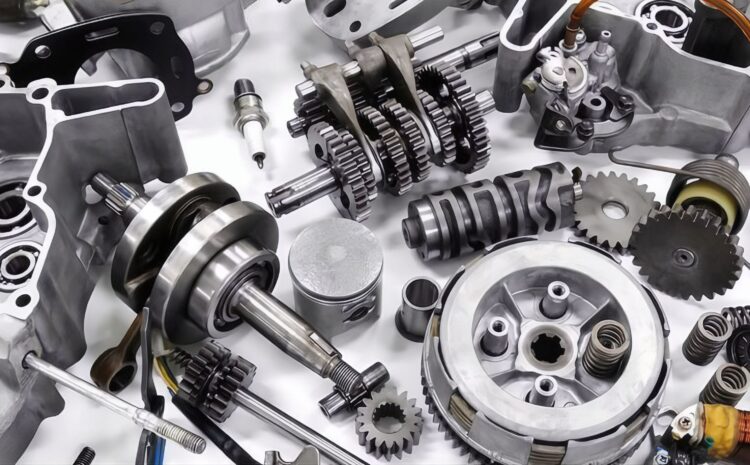
HIGH COST OF USING SUBSTANDARD PARTS
Diesel engines are a leading choice for prime movers and industrial applications due to their operational robustness and efficient performance. They are widely used in power generation, construction machinery, military equipment, and trucks. Their use in critical applications makes their reliability a crucial operating requirement. Due to the nature of their job, they must always be maintained in operational condition. Companies usually take the Preventive Maintenance (PM) strategy for that. This strategy means regularly scheduled maintenance, timely engine overhauling, and replacement of worn-out parts.
The preventative maintenance strategy requires that the components be discarded at the end of their useful life so they would not cause serious damage to the allied parts. Replacing engine parts is a costly exercise and many machine owners tend to pick the cheapest available parts for it. The approach may seem budgeted, but it can cause serious damage to the overall performance and increase the financial cost.
The failure of engine components is highly interactive. One damaged component can cause a chain of failures. Sometimes, the fault only requires the replacement of one or two minor parts. However, if the part is of low quality, it may cause serious damage to the allied components and you may end up replacing all the major components of your machine.
WHY ENGINE FAILS TO WORK PROPERLY:
The common problems associated with substandard spare parts are improper fitting, poor casting, and inappropriate material.
IMPROPER FITTING:
Engine components work under extreme conditions like high temperature and pressure. They must be manufactured with appropriate material, suitable for the working conditions. If any of the cylinder components like piston, ring, or connecting rod cracks, it disengages and collides with the rotating assembly. A series of high-energy collisions can create a high degree of secondary damage to the engine assembly.
CASTING ISSUES:
These parts have rough surfaces and pinholes and abrasive particles on top. When they work under extreme temperature and pressure in a cylinder, they contaminate it with abrasive particles. These could damage all the moving parts in the combustion chamber. First, it wears off the piston rings and reduces its ability to seal the cylinder sufficiently. This makes it unable to prevent oil from passing into the combustion chamber. Which ultimately increases the pressure in the crankcase and causes multiple other damages.
INAPPROPRIATE MATERIAL: If you are to rebuild your engine for a second life, you must ensure that every component meets the high-quality standard. HDP engine parts are manufactured with high precision and OE specification. All of our parts work together as a complete unit. They are manufactured to withstand the high demands of the diesel engine.